Why Your Inventory Management Needs Bill of Materials (BOM)
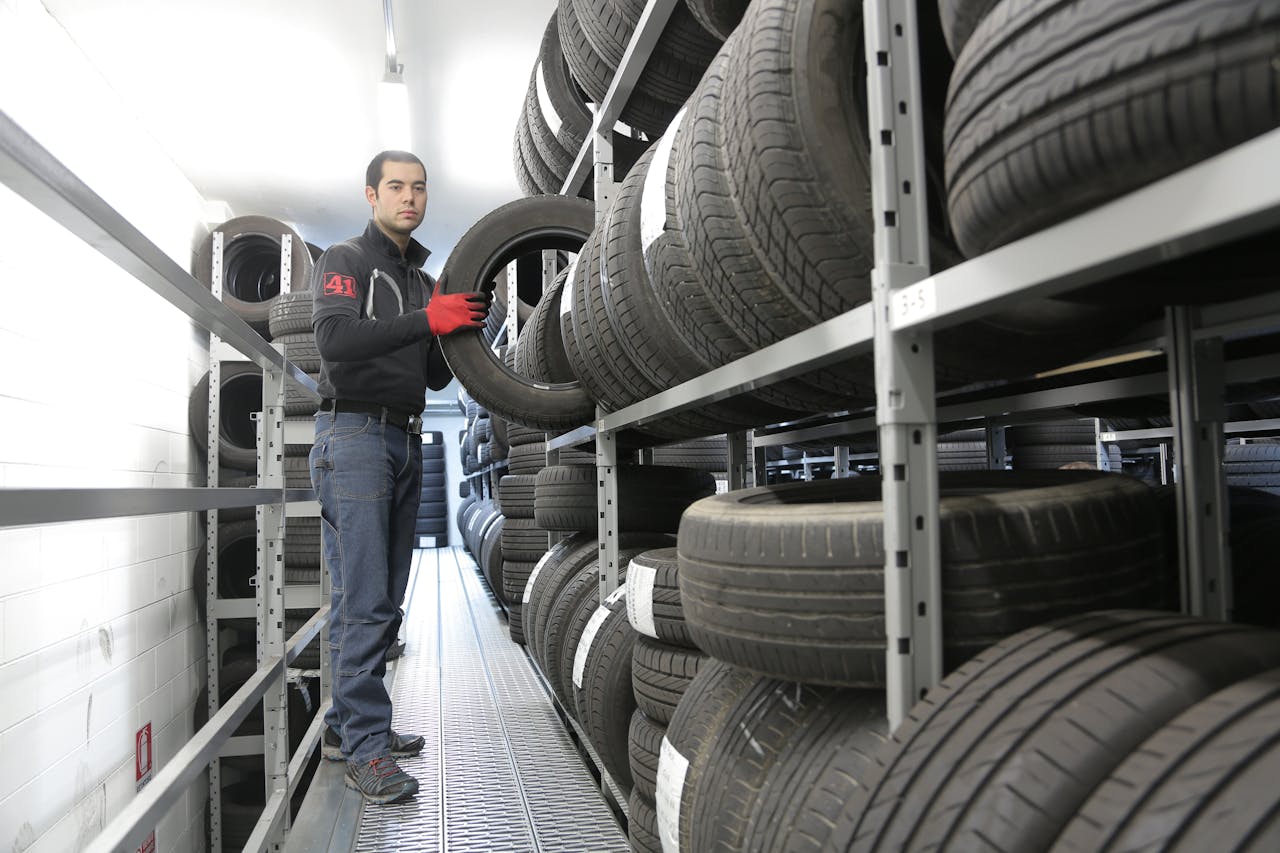
Managing inventory is about more than just tracking stock levels. For businesses that deal with manufacturing, assembly, or custom products, understanding what goes into each product is crucial. This is where the concept of Bill of Materials (BOM) comes into play.
In this article, we’ll explore the importance of BOM in inventory management and how having BOM software—like Flip Inventory—can make all the difference in ensuring smooth operations, reducing errors, and improving your bottom line.
What is a Bill of Materials (BOM)?
A Bill of Materials (BOM) is essentially a detailed list of all the raw materials, components, sub-assemblies, and other parts that are needed to manufacture a product. It’s the blueprint for creating a product, outlining everything from the smallest screw to the most complex assembly.
In simpler terms, it’s a recipe for your product. For a bakery, a BOM would list flour, sugar, eggs, etc. For a tech company, it might include specific microchips, sensors, or screws required to build a device.
The Role of BOM in Inventory Management
In inventory management, having a BOM provides visibility into every element that makes up your final product. This visibility ensures that materials are available when they are needed, and also helps track the usage of materials over time.
Here’s how BOM impacts inventory management:
Material Requirement Planning (MRP): By having an accurate BOM, you can plan ahead for materials, order them in advance, and avoid stockouts. Efficiency in Production: BOMs provide a clear understanding of what components are needed and when. This can significantly speed up the manufacturing process and reduce downtime. Cost Control: By tracking the exact materials needed for each product, you can better estimate costs and avoid wastage.
Key Components of a Bill of Materials
A BOM isn’t just a list of materials—it also includes important details like:
Quantities: How much of each material or part is required. Part Numbers: Unique identifiers that ensure the right materials are sourced. Description: A short description to clarify what each part is. Units of Measure (UOM): How the material is measured (e.g., kilograms, meters, pieces). Each of these elements plays a crucial role in making sure the product is produced as intended, without delays or errors.
Why Every Business Needs BOM Software
If you’re still manually managing your BOMs with spreadsheets or paper, you’re leaving room for inefficiencies and errors. That’s where BOM software comes in.
Businesses today rely on specialized software to streamline their operations, and BOM software is no exception. Here’s why your business needs a BOM management tool:
Improved Accuracy
When you use software to manage your BOM, you eliminate the chances of manual data entry errors, which can be costly. BOM software automatically updates when materials are used or when stock levels change, ensuring that all information remains accurate in real-time.
Streamlined Production Planning
BOM software helps businesses plan ahead by showing exactly what parts are required for a production run. You can track inventory levels, ensure materials are ordered in advance, and even plan out production schedules based on available materials.
Reduced Costs and Waste
By optimizing material usage through accurate BOM management, businesses can reduce material wastage and lower costs. With precise BOMs, you can predict exactly how much of each material is needed, ensuring you don’t over-order or waste valuable resources.
Flip Inventory’s BOM Feature
Flip Inventory is designed to help businesses stay organized, and its BOM feature is a game changer for those managing inventory with complex product assemblies. The BOM module in Flip Inventory helps you manage and track all the parts required for each product and integrates directly with your inventory system for seamless updates.
Managing BOM within Flip Inventory
With Flip Inventory, you can easily create and manage your BOMs within the app. The interface is user-friendly, allowing you to add parts, manage quantities, and track usage without the hassle of spreadsheets or paper records.
By using Flip Inventory, you can:
- Track parts in real-time: Know exactly what’s in stock and what needs to be ordered.
- Automate BOM updates: Changes to materials or quantities are automatically reflected across the system.
- Organize BOMs by product: Each product has its own BOM, making it easy to find exactly what’s needed for each assembly.
Benefits of Integrating BOM with Inventory
The true power of BOM software lies in its integration with your inventory system. With Flip Inventory, you get real-time updates on stock levels, ensuring that you’re never caught off guard by low inventory or delays in production. Read more about How to Prevent Stockouts and Overstocking with Inventory Tracking Software.
The BOM integration means:
Accurate material forecasting: You’ll know exactly how much stock you need for production runs, helping you avoid stockouts and production delays. Efficient supply chain management: When materials are tracked and accounted for, suppliers can be managed more efficiently, and purchasing decisions can be made based on actual needs, not assumptions.
How Flip Inventory Enhances Your Business Operations
Beyond managing BOMs, Flip Inventory offers a suite of features designed to streamline your entire business operation, from inventory tracking to order fulfillment.
Accurate Stock Tracking and BOM Integration
With Flip Inventory, your inventory levels are updated automatically as materials are used in production. This ensures that your BOM always reflects accurate stock levels, making inventory management more reliable and efficient.
Order Fulfillment with BOM
When an order comes in, Flip Inventory’s order fulfillment feature ensures that the right products are packed and shipped. By integrating your BOM with the order fulfillment process, you can ensure that the correct components are used, avoiding mistakes or discrepancies in the final product.
Conclusion
In today’s fast-paced business world, Bill of Materials (BOM) management is no longer optional—it’s essential. Accurate BOMs help you reduce costs, streamline production, and improve your overall inventory management process. By integrating BOM software like Flip Inventory, you can ensure that your business stays organized, efficient, and ready to scale.
FAQs
- What is a Bill of Materials (BOM)?
A BOM is a detailed list of all the materials, parts, and sub-assemblies required to produce a finished product. Why should I use BOM software?
- BOM software helps improve accuracy, reduce errors, streamline production, and minimize costs by providing real-time updates and better material tracking. Can I track BOMs with Flip Inventory?
Yes, Flip Inventory has an integrated BOM module that allows you to manage, update, and track all the materials and parts needed for your products. How does BOM software help with inventory management?
- BOM software helps businesses manage their inventory by providing visibility into material requirements, optimizing stock levels, and reducing waste. Can Flip Inventory help with order fulfillment?
Yes, Flip Inventory’s order fulfillment feature works seamlessly with the BOM module to ensure that the right materials and products are packed and shipped efficiently. Read more How Order Fulfillment Boost Efficiency and Customer Satisfaction